Making a furniture panel at home with your own hands, the subtleties of the process
Furniture board is a specific type of wood materials created by gluing standard planed wooden blocks. It is effectively used to create various types of fittings and coatings. It’s not difficult to make a furniture panel with your own hands at home, so this work is available for everyone to do independently. The resulting structures are natural and environmentally friendly, and at the same time much more attractive than particleboard or MDF.
Selection and preparation of materials
Creating a furniture panel with your own hands at home involves the use of different types of wood. Most often, birch or oak, beech or aspen, as well as larch and various conifers are used for this.
Each tree species has its own characteristics, therefore, before making a certain choice, it is recommended to determine in advance in what operating conditions the resulting contraction will be applied.
Most often, furniture panels are used to create different furniture and doors. They are distinguished by the presence of a specific internal voltage, therefore, in the process of work, one must be careful not to violate the integrity of the structure. Incorrect work can lead to deformation of the finished product.
The main advantages of furniture panels are:
- environmental cleanliness due to the use of natural components and high-quality glue;
- the refined appearance of the resulting furniture and other designs, but this is possible only with the competent processing of panels;
- high practicality, as the wood has a homogeneous structure, which allows you to restore broken or lost attractiveness elements;
- the manufacture of furniture panels is an incredibly simple task, and at the same time a small amount of money is spent on this process;
- furniture made of panels is durable and attractive;
- products do not have any cracks or other deformations, and also do not undergo significant shrinkage.
The main factor in obtaining a high-quality shield is a competent choice of material for these purposes. As standard, furniture panels have a thickness of 2 cm, therefore, prefabricated pieces of optimal size, as well as having the desired thickness, are initially prepared. Since the boards will certainly have to be planed, and then sanded, they should be purchased with a margin, so their thickness should be 2.5 cm.
In the process of choosing a material, one should focus on the type of wood, as well as on the quality of the boards. Wood is not allowed to be uneven or warped. It should be of high quality, properly dried and with a complete absence of any rotten areas. Therefore, before purchasing, you should carefully inspect the boards. Additionally, the supporting documentation for the material is studied in detail.
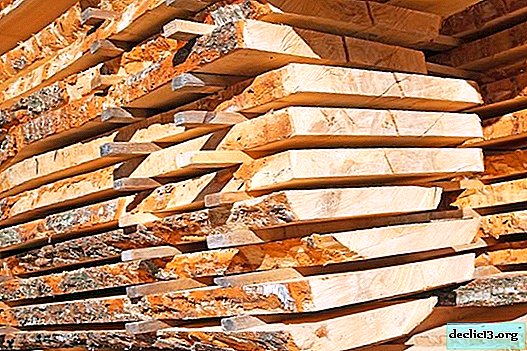
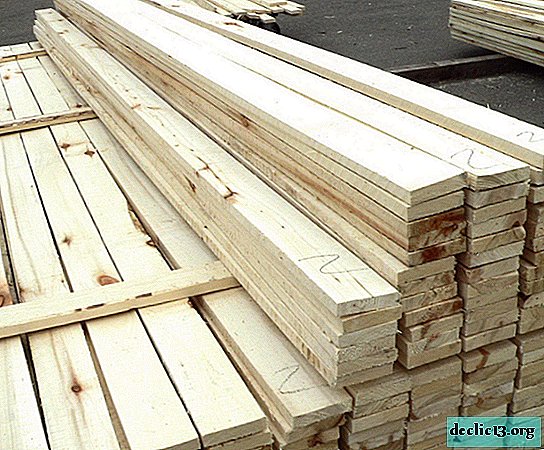
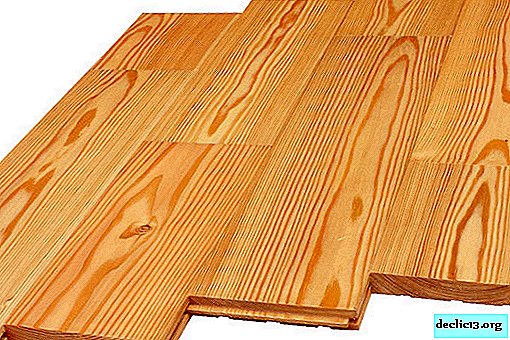
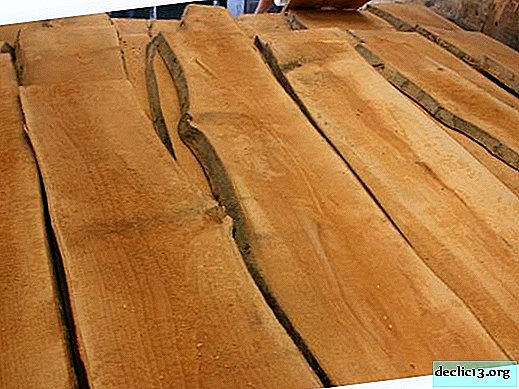
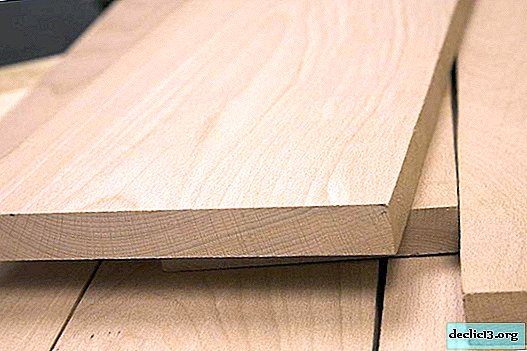
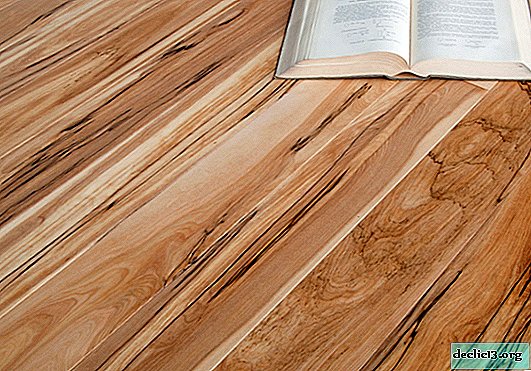
Necessary tools
Do-it-yourself gluing of the furniture board is done using standard tools. Usually they are available for every man who prefers to do numerous housework on his own. Therefore, only elements are prepared:
- Planer for optimal wood preparation
- tool for joining and gluing individual wooden blocks;
- belt type grinding machine;
- the construction level, which allows you to get really flat boards;
- coarse sandpaper;
- flat grinding machine.
These tools will be enough to make a shield, so no expensive devices will be needed anymore.
Manufacturing rules
As soon as the tools are completely ready for the planned work, the direct production procedure begins. How to make a furniture board? This process is not considered too complicated, but in order to eliminate possible errors or problems, it is recommended that you study the correct instructions in advance. For this, sequential actions are performed:
- initially, wooden boards are cut into individual bars having the right size, and it is important to cut so that they are strictly at right angles;
- any irregularities or other defects are not allowed, since in this case it will not be possible to glue the furniture board correctly;
- if slight distortions are found, then they can be eliminated with a conventional planer;
- an important moment in production is considered to be the combination of the obtained blanks, since they should be the same in texture and color, as well as in other important parameters;
- after the selection of elements, they are marked so that during gluing there would be no difficulties with their correct location.
In order for all stages of the process to be carried out taking into account the main nuances, it is recommended to watch the training video in advance.
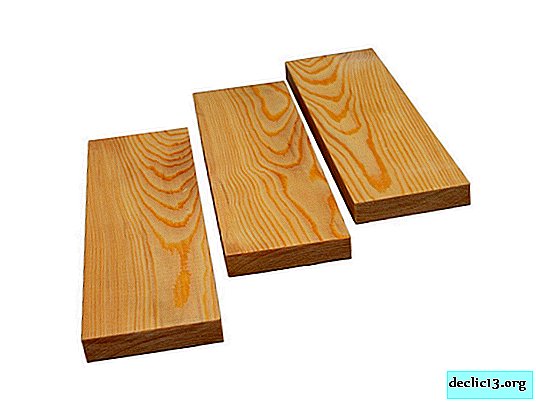
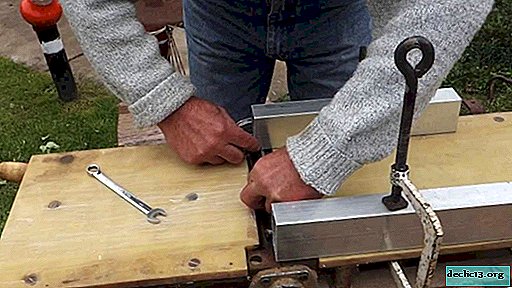
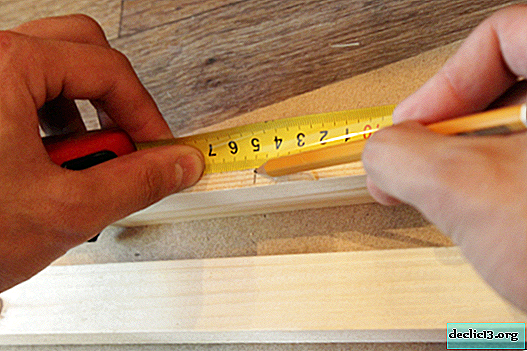
Bonding technology
After all the made bars have been prepared, you can proceed to their direct gluing, which will ensure a high-quality shield. This procedure is also divided into successive stages:
- a device is selected that makes it possible to glue the bars, and it should be smooth, and usually a regular chipboard sheet is used for this;
- at the edges of the sheet, strips are fixed, and their height depends on the parameters of the prepared bars;
- bars are laid out between these slats, moreover, they should fit snugly against each other and an attractive pattern of them should be formed;
- if there are cracks, then they can be easily removed with a standard jointer;
- then the bars are glued together, for which different types of glue intended for wood are used, but the use of PVA glue is considered optimal;
- with glue, the entire surface consisting of bars is completely smeared, and it is important that the product is evenly distributed over the surface;
- lubricated elements are pressed tightly against each other;
- on the strips, fixed to the chipboard sheet, two more such strips are laid, after which these elements are connected by self-tapping screws, and this is necessary to prevent the resulting shield from bending;
- the resulting workpiece is left for about an hour, after which the shield is released and left for a day.
Thus, having figured out how to glue the elements to obtain a furniture panel, this process will not require significant effort. The procedure is easily implemented on its own, and as a result, designs are obtained that are effectively used to create numerous furniture, doors or even full-fledged coatings, which are not only highly durable, but also reliable and have an attractive appearance.
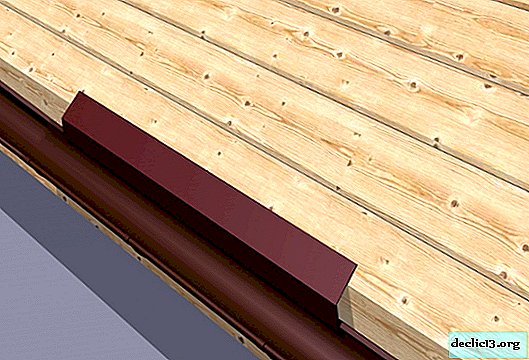

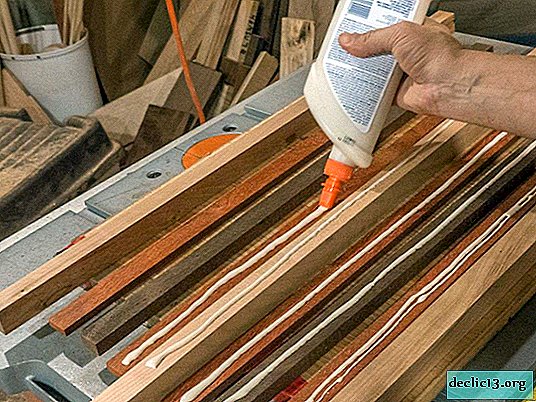
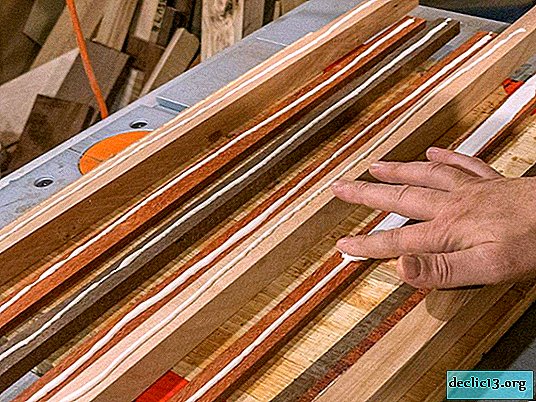
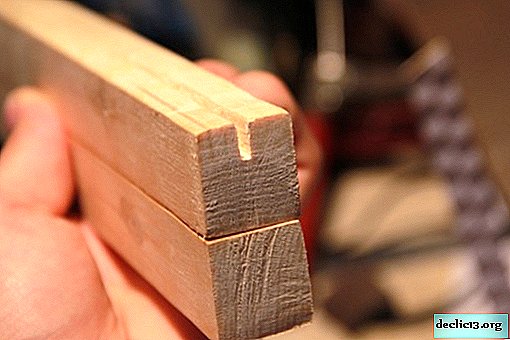
Final processing
Shields are made in such a way that they are not only strong and durable, but also quite attractive. For this, attention is paid to some of the finishing stages, which include special processing. To do this, the following actions are performed:
- a preliminary grinding procedure is carried out. For these purposes, it is recommended to use a standard belt sander. A special emery paper must be inserted into it, and it should have large fractions, since the initial processing is done. It allows you to eliminate large defects and differences that remain on the surface after the process of creating a shield. It is necessary to act carefully, and the process is carried out in consistent and even lines;
- secondary processing - involves the use of a flat grinder. It provides removal of the slightest differences, irregularities and other defects present on the surface of a wooden furniture panel. Also due to this process, the pile is removed from the surface. It is recommended to pre-moisten the base with a small amount of water, and grinding should begin only after the structure has completely dried.
After properly implemented processing, it is possible to use the resulting shields to create a variety of tables or shelves, cabinets and other furniture. It is allowed to use them for the formation of doors or coatings with high strength, reliability and durability.
Thus, furniture panels are quite popular and sought after designs. They are used to create numerous interior items. If desired, and the availability of time and opportunity, you can make such shields with your own hands. For this, different materials are used, represented by different types of wood. They are subjected to special processing, and then glued to each other using special technology. This ensures a truly high-quality, durable and attractive shield used for various purposes. To give it high strength and reliability, we must not forget about the special processing performed after the procedure for creating the structure.

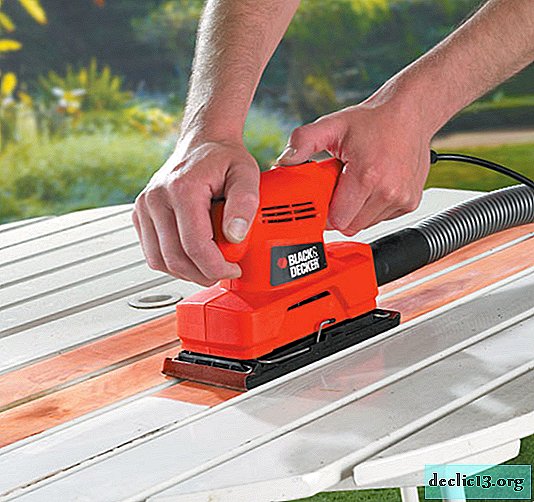